배터리 생산 수직 계열화 인동첨단소재 유성운 대표
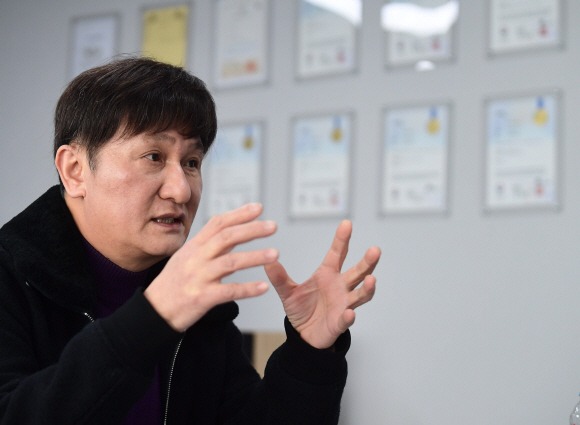
배터리 생산 수직 계열화에 나선 스타트업 인동첨단소재의 유성운(57) 대표를 최근 서울 서초구 서운로의 서울사무소에서 만났다. 최근 각광받는 2차전지 산업을 LG에너지솔루션이나 삼성SDI와 같은 대기업이 아니어도 할 수 있는지 반신반의하면서 찾았다.
우리가 먹거리로 삼는 배터리의 음극재는 전기를 저장하고 배터리의 수명을 결정하는 핵심 소재로 흑연이 주요 원료다. 배터리 가격의 18%를 차지한다. 시장조사 업체 SNE리서치에 따르면 연평균 39% 성장해 2025년엔 글로벌 음극재 수요가 135만 8000t으로 예상된다. ‘미래는 배터리를 가진 자가 세상을 지배한다’고 하지만 현재 전 세계에서 중국만 유일하게 음극재용 흑연 중간재를 생산한다.
‘중국만 생산한다’는 말에 고개를 갸웃거리자 유 대표는 “흑연은 우리나라뿐 아니라 세계 곳곳에 있는 흔한 광물이지만 음극소재 가공 처리를 하지 못한다”며 설명을 이어 갔다. “흑연을 음극재로 만들려면 머리카락 절반 두께인 40㎛(마이크로미터·100만분의1m) 이하로 부숴 흑연에 섞인 불순물을 걸러내야 한다. 이 과정에 염산·황산·불산 등의 독극물 수준의 화학물질이 사용되기에 중국에서도 방독면을 쓰고 작업한다. 산(酸)처리를 한 다음엔 흑연을 물로 씻는 작업 탓에 공기와 강이 심하게 오염된다. 이런 이유로 우리나라뿐 아니라 선진국에서는 흑연 가공 공장 설립 허가가 나지 않는다.” 일전에 외신에서 본 중국의 흑연 가공장 옆에 대규모 화학공장과 커다란 강이 있는 이유를 알 듯했다.
국내에서 흑연 음극소재를 만들겠다는 것은 결국 우리의 강과 공기를 오염시키는 것이 아니냐고 도발했다. 그의 답변이다. “다른 기업들은 흑연을 분쇄하면 그 굵기가 5~300㎛로 균일하지 못하다. 흑연 알갱이 크기가 40㎛ 이하만 활용하고, 나머지는 70% 정도 버려진다. 폐기되는 흑연을 우리 분쇄기에 넣었더니 크기가 1㎛로 균일하게 나왔다. 잘게 부서지면서 흑연 속의 불순물도 자연스레 분리됐다. 그러니 산처리를 하거나 세척 과정이 필요하지 않게 된 거다. 경북 포항시에 공장 부지 2만 2000평을 확보했고, 10GW(기가와트) 규모의 생산 공장 착공을 준비하고 있다. 음극재 생산이 무산되면 우리 배터리 산업은 중국에 휘둘리는 인질이 될 수 있다.” 흑연을 미세하고 균질하게 분쇄한다는 것은 쉬운 기술이 아니란다. 탄소로 구성된 흑연의 단단함은 다이아몬드와 같기 때문이란다.유 대표의 사업 출발은 방열(放熱) 시트 제조였다. 온갖 전자 제품이 작동하는 동안 발생하는 열을 밖으로 빼 식히는 방열 제품인 방열 시트를 제조하고자 달려들었다. 기기 내부의 열을 빼내지 못하면 오작동과 폭발 위험이 따르기 때문이다. 방열 소재로 열 전도성이 뛰어난 흑연이 제격이지만 결정적인 걸림돌이 있었다. 방열 시트는 미국 N사가 천연 흑연으로 만드는 특허 506개를 걸어 두고 독점적으로 생산하고 있다. 흑연으로 이 회사의 특허를 피해 방열 시트를 만드는 건 사실상 불가능했다.
이를 고민하던 유 대표는 2013년 여름 우연히 TV에서 포스코 용광로에서 흘러나오는 붉은 쇳물 위에 거뭇거뭇 뜬 부산물을 보고 ‘저건 용광로 열에 어떻게 견딜까’ 생각하다 가져와 성분을 분석했다. “분석해 보니 탄소가 99.97%였다. 고순도 탄소 덩어리였다. 이를 갈아 방열 시트를 만들고자 했지만 잘게 부술 수가 없었다. 탄소는 강철보다 7배 이상 단단하기 때문이다. 일본 분쇄기로 갈아 봤지만 오히려 기계가 망가졌다. 이때부터 탄소 덩어리를 분쇄하는 기술을 찾아 연구에 매달리다 3년 만에 성공해 원천 기술을 확보했다. 방열 시트인 복합 그래파이트를 만드는 데 성공했다. 흑연이 아니어서 경쟁사의 특허 침해의 소지도 없었다. 그러곤 2017년 4월 회사를 설립했다. 산업 부산물을 가공해 만든 우리 방열 시트의 두께는 100~1000㎛로, 주로 프리미엄 TV에 사용되며 노트북·게임기에서부터 전기차에도 쓸 수 있다. 올해 출시되는 8K TV에도 들어간다. 방열 시트는 향후 급성장이 예상돼 생산 확대도 고민하고 있다.”
탄소 덩어리를 잘게 가루 내는 이 분쇄기가 유 대표의 ‘보물 1호’다. 수많은 기술을 특허 등록했지만 이 분쇄기만큼은 특허 출원을 하지 않았고, 하지 않겠다고 했다. “특허 등록하는 순간 우리 기술이 고스란히 노출된다. 특허를 훔쳐 쓴 회사와 소송이라도 가면 수년이 걸린다. 그동안 중소기업인 우리는 진력이 다 빠진다. 상처뿐인 승리가 되지 않겠나. 지금도 분쇄기의 기술 탈취 시도가 끊임없이 이어진다.”
그가 부산물로 버려지는 흑연을 이 분쇄기에 넣었더니 곱고 균일하게 갈렸다. 이렇게 해서 음극재를 생산하는 회사가 되겠다고 나선 것이다. 특히 흑연 음극재에 실리콘을 섞으면 배터리의 용량이 크게 증가한다는 것은 학계에 알려진 사실이다. “실리콘을 코로나 바이러스 크기인 50nm(나노미터·10억분의1m)로 분쇄하는 것이 관건이다. 흑연보다 입자가 작아야 잘 섞이기 때문이다. 실리콘을 우리 분쇄기에 넣었더니 50~100nm 크기로 갈렸다. 2세대 배터리인 ‘실리콘 음극재’ 배터리 시제품을 만들었고, 국내외에서 인증받았다. 대용량 배터리에 필요한 실리콘 음극재를 공급하기 위해 2020년 FIC신소재라는 회사를 설립했고, 현재 포항에 양산 설비를 갖추고 있다.
그는 음극재의 궁극적인 기술인 ‘구상조립흑연’을 완성했다고 강조했다. “구상조립흑연은 기존 흑연보다 리튬이온의 이동 거리를 줄여 고출력 충전 및 방전이 가능하다. 전기차용 배터리에 적용하면 충전 시간이 획기적으로 단축된다. 순간적으로 큰 출력을 내야 하는 대형 트럭이나 버스도 전기차로 전환이 가능한 기술이다.” 대량생산된다면 배터리 산업에 지각변동을 불러올 기술로 보인다. 그는 배터리 완제품을 만드는 회사도 2018년 설립했고, 수도권에 공장 설립 부지를 찾고 있다. 배터리 음극재부터 완제품 생산까지 수직 계열화를 통해 최고의 배터리 제조 회사가 되겠다는 포부를 보였다.
사업을 하면서 가장 어려웠던 점을 묻자 유 대표는 “대기업도 못하는데 ‘고졸이 뭐 하겠나…’라는 시선과 ‘속임수 아냐’라는 말”이라고 털어놓았다. 하지만 그의 실력은 외국에서 먼저 인정받았다. 지난해 4월엔 영국 국영 배터리 산업화센터(UKBIC)의 초청을 받기도 했다.
“돌고 돌아 배터리 제조로 왔다. 운명 같다. 고졸이지만 20대 때 수백억원을 모았다. 공부할 필요가 없었던 거다. 대학을 마치지 않았지만, 호기심이 생기면 몇 년씩 끝까지 파고든다. 외국 논문도 읽고, 기계를 직접 만든다. 이게 공부 아닌가.”
<저작권자 ⓒ 매일한국, 무단 전재 및 재배포 금지>
박세인 기자 다른기사보기